诸暨八轴精密数控车床加工
精密CNC数控车床加工是现代制造业中不可或缺的一环,它以其高精度、高效率以及强大的灵活性,在众多领域发挥着至关重要的作用。这种加工方式通过计算机程序的精确控制,能够实现复杂零件的微米级加工,无论是汽车零部件、航空航天器件,还是精密医疗器械,都能在其精确的操作下完美成型。CNC数控车床采用先进的伺服驱动系统和闭环控制系统,确保了加工过程中的稳定性和可靠性,减少了人为误差,提升了产品质量。此外,其强大的编程功能使得加工过程可以灵活调整,适应不同批次、不同规格的产品需求,有效降低了生产成本,提高了生产效率。随着技术的不断进步,精密CNC数控车床加工正向着更高精度、更高效率、更智能化的方向发展,为制造业的转型升级提供了强有力的支持。精密数控车床加工可以实现自动工件传送,减少人工操作。诸暨八轴精密数控车床加工
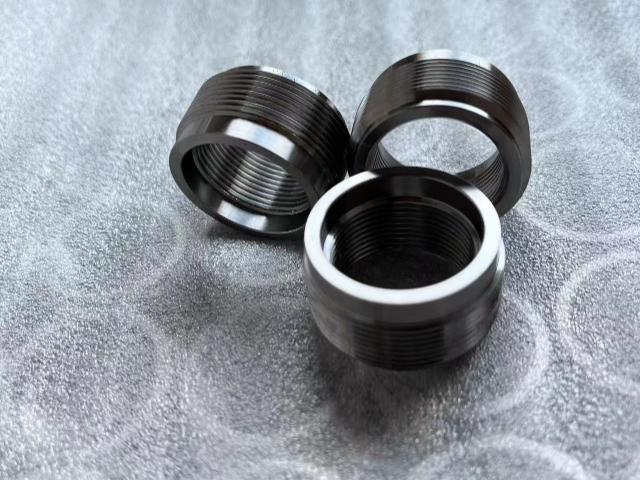
随着科技的不断进步,零件的精密数控车床加工技术也在持续革新。现代数控车床不仅具备更高的加工精度和效率,还融入了智能化、网络化的元素。通过集成传感器和数据分析系统,能够实时监控加工过程中的各种参数,如切削力、温度、振动等,及时发现并纠正潜在的加工误差。同时,借助云计算和物联网技术,远程监控和故障诊断成为可能,缩短了设备维护和故障排除的时间。此外,随着人工智能技术的应用,数控车床的加工策略得以不断优化,进一步提升了加工效率和材料利用率。这些创新技术的应用,使得精密数控车床加工在制造业中的地位日益凸显,成为推动产业升级的重要力量。海宁cnc精密数控车床加工公司精密数控车床加工可实现高精度、高效率的螺母加工。
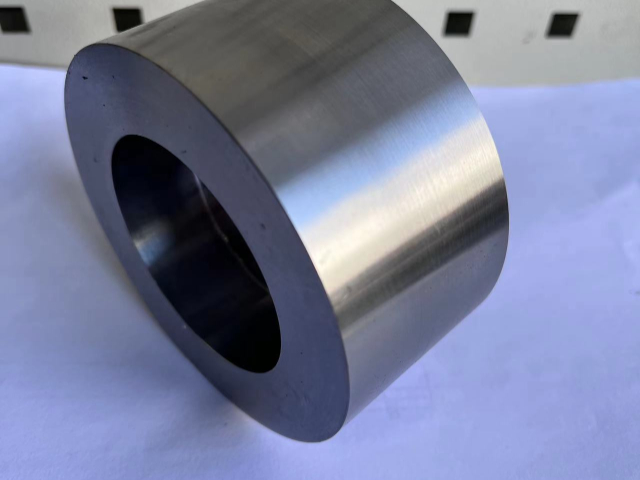
随着科技的进步,大型数控精密车床加工技术也在不断革新。现代车床普遍配备了智能传感系统和实时监控功能,能够实时检测刀具磨损、工件变形等异常情况,并自动调整加工参数,确保加工过程的稳定性和安全性。同时,随着物联网、大数据等技术的融合应用,大型数控车床的加工数据可以被实时采集和分析,为生产优化和工艺改进提供了强有力的数据支持。此外,一些高级车床还引入了人工智能算法,能够自主学习和优化加工策略,进一步提升加工效率和精度。这些技术的引入,使得大型数控精密车床加工在智能制造的新时代中,展现出了更加广阔的应用前景和巨大的发展潜力。
卧式精密数控车床加工是现代制造业中不可或缺的一环,它凭借高精度、高效率以及高自动化的特点,在众多领域内发挥着重要作用。这种车床采用卧式设计,使得工件在加工过程中能够更加稳定,有利于实现复杂形状和精密尺寸的加工需求。通过先进的数控系统,操作人员可以精确控制车床的各个运动轴,实现微米级的加工精度,这对于航空航天、医疗器械以及精密电子等领域来说至关重要。此外,卧式精密数控车床还具备强大的编程和数据处理能力,能够轻松应对大批量、多种类的生产任务,提高生产效率的同时,也降低了对人工操作的依赖,进一步提升了产品的质量和一致性。因此,卧式精密数控车床加工不仅标志着现代制造业的发展方向,也是企业提升竞争力的重要手段。精密数控车床加工可以实现自动工艺记录,方便生产管理。
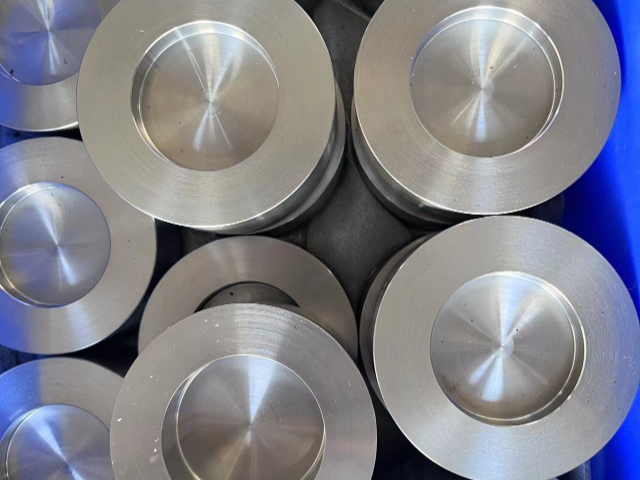
CNC小型精密数控车床加工是现代制造业中不可或缺的一环,它以其高精度、高效率的特点,在众多领域中发挥着重要作用。这种加工方式利用先进的计算机数控技术,实现了对加工过程的精确控制。小型精密数控车床适用于加工小型、复杂且对精度要求极高的零部件,如航空航天领域的精密零件、医疗器械中的关键组件以及电子产品中的微型结构件等。其加工过程稳定可靠,能够有效减少人为误差,提高生产效率和产品质量。此外,CNC小型精密数控车床还具备较好的灵活性和适应性,能够轻松应对不同材质、不同形状的零件加工需求,满足客户的多样化定制要求。随着科技的不断进步,CNC小型精密数控车床的加工技术和设备性能也在持续提升,为制造业的发展注入了新的活力。数控车床加工可以实现高精度加工,满足各种精度要求。宿迁三轴精密数控车床加工
精密数控车床加工可以实现自动工件夹紧,提高加工效率。诸暨八轴精密数控车床加工
精密数控车床加工是现代制造业中不可或缺的一环,它凭借高度自动化和智能化的特点,明显提升了零件加工的精度与效率。这种加工方式通过计算机程序的精确控制,能够实现微米级甚至更精细的加工,满足航空航天、医疗器械、精密仪器等高技术领域对零部件的严苛要求。在加工过程中,精密数控车床不仅能够完成复杂的三维曲面加工,还能通过多轴联动技术,一次性完成多面加工,缩短了生产周期。此外,其内置的传感器和监控系统能够实时反馈加工状态,及时调整加工参数,确保每一件产品都能达到设计标准,有效降低了废品率。这种高精度、高效率的加工方式,不仅推动了制造业的技术进步,也为实现智能制造奠定了坚实的基础。诸暨八轴精密数控车床加工
上一篇: 邳州专业精密数控车床加工价格
下一篇: 海安附近的精密数控车床加工厂